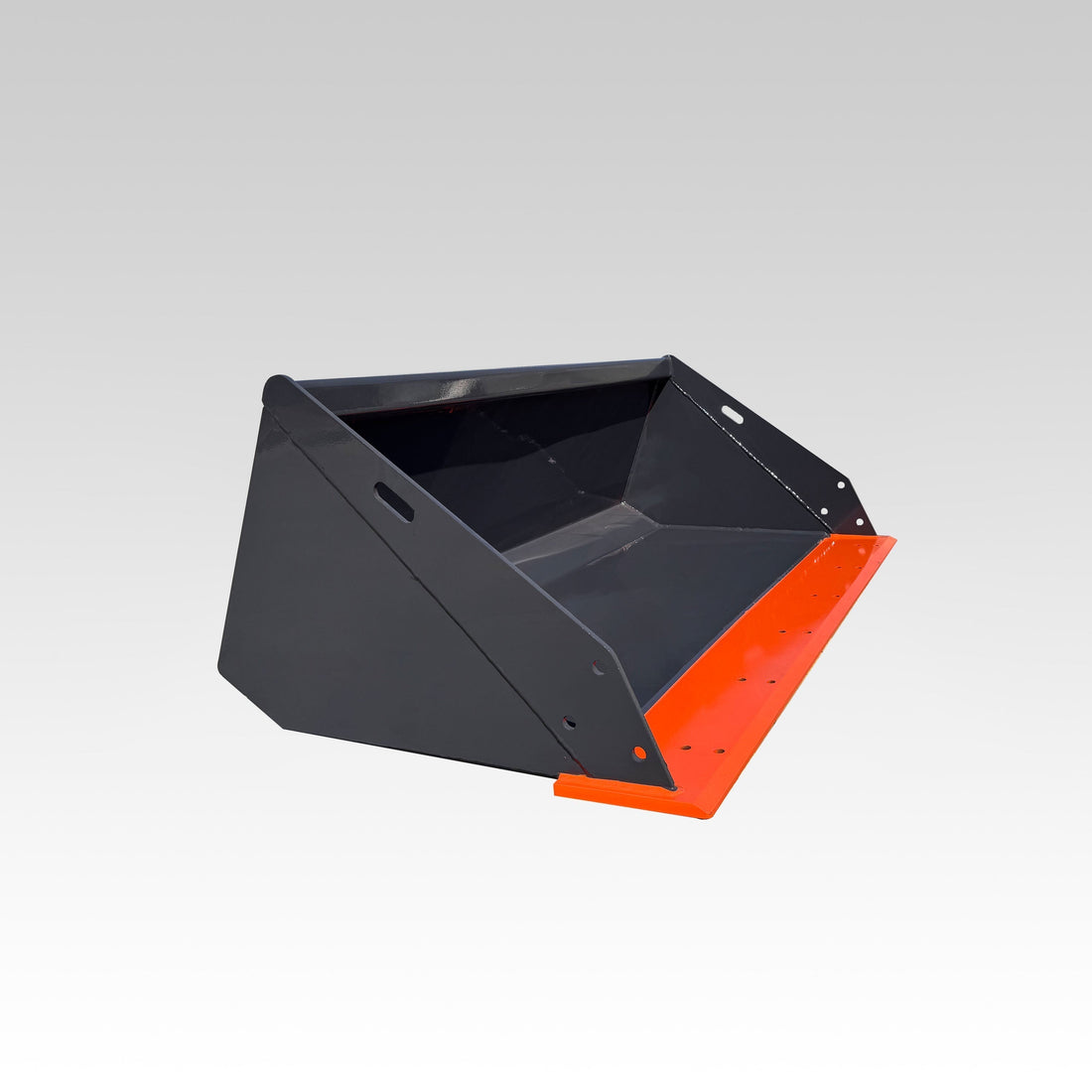
Beyondtech Insight: Why a Universal Skid Steer Bucket Still Reigns as the Job-Site MVP
Share
1. Introduction – The Swiss-Army Knife of Compact Equipment
Scroll through any rental catalog or contractor’s yard and you’ll find dozens of specialty attachments: trenchers, cold planers, grapples, brooms. Yet the first tool every operator reaches for remains the universal skid steer bucket. Call it a standard bucket attachment, a skid steer general purpose bucket, or even a multipurpose skid steer bucket—the concept is the same: one rugged scoop that loads, digs, levels, grades, and cleans without breaking a sweat.
At HCN we manufacture buckets tough enough for Manitoba frost heave and Arizona basalt alike. In this comprehensive guide we’ll explain how design features such as a ¾-inch × 6-inch high-carbon cutting edge, a robot-welded cast mounting frame, and a channel-formed bucket body translate into real-world uptime. By the end you’ll know how to compare brands, match capacity to your loader’s breakout force, and spec the best standard bucket for skid steer fleets from landscaping start-ups to multistate earth-moving giants.
2. Anatomy of a HCN Standard Bucket
Component | What It Does | Why It Matters |
---|---|---|
¾-inch × 6-inch cutting edge | Slices into virgin soil, pry-bars rock, and resists curb rash. | Thicker edge means fewer costly blade swaps. |
High-carbon cutting edge | Holds a keen profile longer than mild steel. | Less downtime grinding or flipping edges. |
Cast mounting frame | Integrates quick-attach hooks in one solid piece. | Removes weak weld seams; boosts torsional rigidity. |
Channel-formed bucket shell | Wraps plate into a structural “C.” | Distributes impact loads, sheds sticky clay. |
Round back design bucket | Promotes smooth “rollout” when dumping. | Cleaner emptying = faster cycle times. |
Reinforced high-strength steel side plates | Absorb shock from stump roots and rebar. | Extends life in demolition or quarry work. |
Heavy-duty welds with robotic pulse arcs | Penetrate deeper, cool slower. | Prevents micro-cracks that start around skip welds. |
Together these elements create a durable skid steer bucket with reinforced back that stays square after thousands of hours—a must for precise grading.
3. Performance Metrics That Matter
- High breakout force bucket geometry. Beyondtech keeps the hinge line low and the shell shallow, maximizing leverage so even smaller loaders feel stronger.
- Precision-cutting bucket bevel angle. A machined 18-degree bevel shaves soil cleanly, ideal for laser-guided grading.
- Bolt-on or weld-on teeth options. Swap to a smooth edge for material handling bucket duties—mulch, grain, snow—or install tooth bars for frost ripping.
- Water drain holes placed behind the cutting edge. Prevents freeze expansion cracks in northern climates.
- Optional spill guard rises 12 inches above bucket lip, increasing heaped capacity when moving light bulk—perfect for manure or bark chips.
4. Core Job-Site Applications
Sector | Bucket Role | Key Benefits |
---|---|---|
Construction site bucket tasks | Excavating footings, stockpiling gravel, backfilling utilities. | One tool limits attachment swaps, boosting job site efficiency. |
Landscaping bucket projects | Topsoil spreading, mulch loading, finish grading lawns. | Round back design leaves a smooth surface needing minimal raking. |
Agricultural bucket work | Feeding silage, cleaning pens, loading bedding. | Abrasion-resistant liners extend life in acidic manure. |
Municipal debris handling bucket duty | Clearing snow windrows, loading salt, storm clean-up. | Fits through alley gates where larger loaders can’t maneuver. |
Bulk material loading in mining & quarries | Sand stockpiling, crusher fines handling. | High-strength steel resists gouges from sharp aggregates. |
Whether you’re pushing clay into a hillside or brooming loose-fill at a recycling center, the HCN loader bucket attachment is a genuine job site efficiency tool.
5. Leveling, Grading & Finish Work – Getting Laser Straight
Builders often think they need a dedicated box blade for laser or GPS grading. Reality check: the precision-cutting bucket can achieve sub-half-inch tolerances if you master these tips:
- Float mode finesse – Drop the arms, apply gentle down-pressure, and drive slowly forward with the bucket rolled slightly back—soil feathering will match any box blade.
- Reverse back-drag – Curl the bucket forward 15 degrees and pull. The smooth edge bucket for material handling doubles as a squeegee, distributing fines into low spots.
- Laser receivers – Bolt magnetic laser sensors to the cast frame; the bucket becomes a low-cost blade substitute for sports-field base prep.
For road contractors, coupling a HCN standard bucket with a trimble laser kit creates a high-performance loader bucket that out-grades larger graders on tight urban infills.
6. Choosing Capacity for Breakout vs. Cycle Times
Selecting the correct heaped volume is a balancing act: undersize the bucket and you waste passes; oversize it and you bog down hydraulics, reducing breakout. Use this rule of thumb:
- Find rated operating capacity (ROC) of your skid steer.
- Multiply ROC by 1.5 to approximate tipping load.
- Select a bucket whose full weight (bucket + material) equals 80 % of tipping load at full curl.
For example, a 2,900-lb ROC loader typically handles a 68-inch bucket of wet topsoil (~3,100 lb) without reaching tip-over. That configuration brings near-ideal cycle efficiency without sacrificing stability.
7. Maintenance: Small Habits, Long Life
- Daily rinse: Dried cement or manure accelerates pitting; a minute with the pressure washer protects the reinforced high-strength steel.
- Edge flip schedule: Rotate or flip reversible edges every 250 operating hours—or sooner if you note bevel deformation.
- Check heel wear: When heel thickness drops 10 %, weld on a wear pad or retire the bucket.
- Inspect weld beads: Hairline cracks? Gouge and re-weld early. The heavy-duty welds accept refurbishment better than thinner commodity buckets.
- Grease coupler pins: Not strictly bucket maintenance, but loose pins skew breakout angles, stressing the cast mounting frame.
Follow that regimen and HCN buckets routinely log 4,000+ hours before refurbishment—double the life of thin-plate imports often marketed as “affordable general-purpose bucket” bargains.
8. Accessory & Upgrade Path
- Bolt-on tooth bars – Convert a smooth edge bucket into a digging monster for compacted caliche.
- Side-cutting plates – Square-shouldered plates broaden the cut, ideal for trench cleanup.
- Bolt-on cutting-edge kits – Keep one spare in the truck; swap in 15 minutes when the grader calls for a crisp edge.
- Poly snow edge – Pop off the steel bar and slot in UHMW for road-salt distribution without scarring concrete curbs.
- Segmented spill guard – Remove or add panels to change heaped capacity on the fly.
These kits mean one HCN bucket can morph from frost-digging earthmoving attachment to finished-grade landscaping bucket before lunch break.
9. Cost of Ownership vs. “Cheap” Imports
A $1,000 offshore bucket might look tempting until you tally:
- Two cracked corners at 600 hrs → $300 welding.
- Worn edge at 900 hrs (non-reversible) → $250 blade + labor.
- Bent quick-tach at 1,200 hrs → $600 downtime + parts.
Total: $1,150 in repairs, plus lost production. Contrast that with a HCN 72” at $1,780 list price but running 2,800 hrs before first edge flip. Your accountant will confirm that “buy once, cry once” is the smart play—especially when heavy clay fines ruin a poured driveway because a cheap bucket warped under load.
10. Safety & Best Practices
Never lift personnel with a bucket—OSHA fines hurt more than downtime.
- Stay within rollback limits; spilled gravel on a downhill grade can push a loader sideways.
- Use spotters when back-dragging near utilities; the bucket hides view of trench edges.
- Mark capacity decals clearly; rental customers may not read manuals.
- Avoid “float drop” from transport height; slamming a full bucket can rip the channel-formed bucket nose seam.
Beyondtech includes reflective capacity decals and a QR code linking to our operator safety video—simple measures that protect crews and gear.
11. Why Contractors Choose HCN
- High breakout force bucket geometry boosts production on underpowered machines.
-
Heavy-duty welds executed by six-axis robots guarantee consistency shift after shift.
- Tiered pricing lets small crews access an affordable general-purpose bucket while corporate fleets spec full-tilt high-performance loader buckets.
- Dedicated parts store: order a replacement edge or heel pad by 3 p.m. and it ships same day.
In short, we designed every standard bucket for sale to earn money, not sit pretty on a dealer rack.
12. Conclusion – A Bucket’s True Worth Is Proven in Dirt
From clearing hurricane debris in Louisiana to backfilling fiber-optic trenches in Ontario, Beyondtech’s multipurpose construction bucket for skid steer loaders has earned its place as a fleet staple. Its rounded back design, ¾-inch × 6-inch cutting edge, and reinforced high-strength steel skeleton transform every gallon of hydraulic flow into productive work—loading, leveling, cleaning, and backfilling faster than any “specialty” attachment array.
So before you gamble on thin gauge imports, remember: down-time foremen and do-overs cost more than premium steel. Choose the durable skid steer bucket with reinforced back and let Beyondtech shoulder the wear and tear, while you bank the profit and reputation.
Ready to dig in? Explore the full range of standard bucket attachments at beyondtechmachinery.ca, call 1-800-BT-BUCKET, or visit one of our demo days across Canada and the U.S. This season, equip your loaders with a bucket built to outlast the job.